Unseen parts: The nightmare of aerodynamic correlation
- -
- -
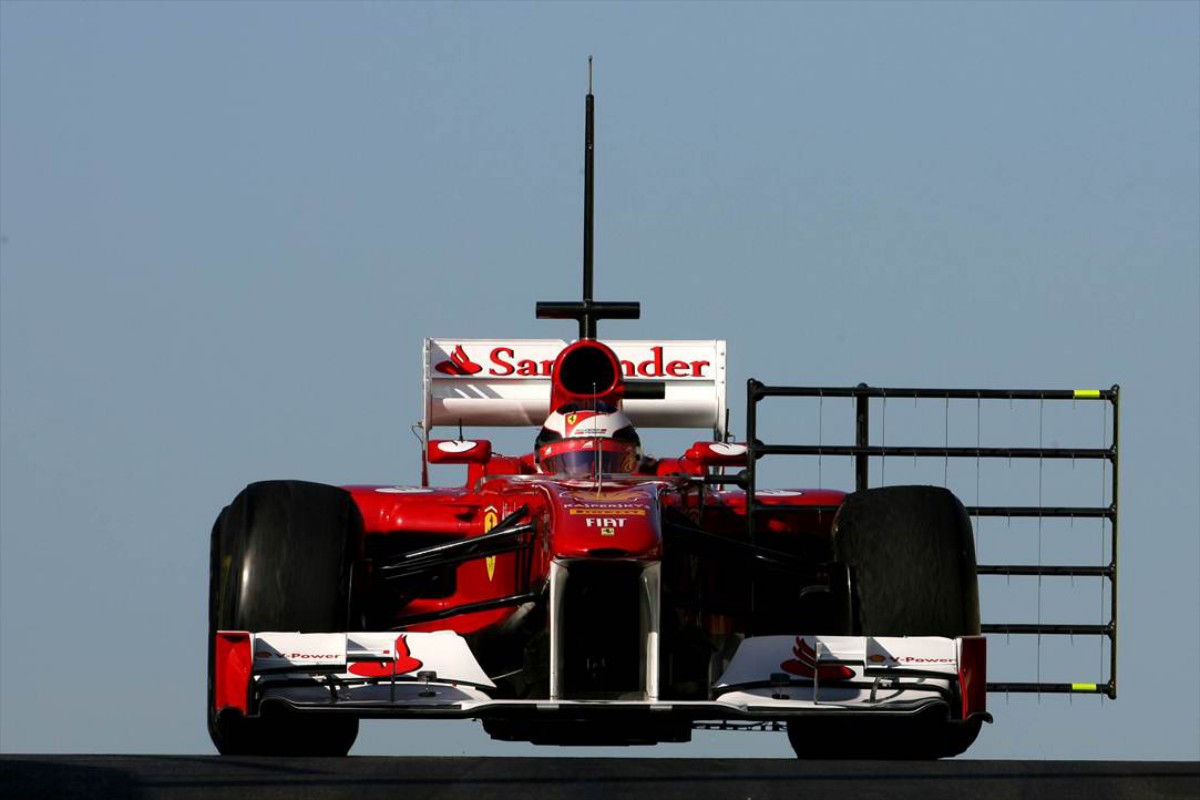
Often there is discussion on “aerodynamic correlation issues” in
the specialist press. Correlation is a strategic aspect to
deal with while developing a F1 car. There then appears
comments in the press like “we are suffering with bad correlation”
or with horrific sentences like “our correlation is lost”.
Eventually, positive comments come out like “our correlation
has improved” and this would magically reset the situation.
My opinion is that the main problem with all this is it leaves the
reader with the impression of talking about a sort of “black
magic”! More seriously, I would not be surprised if the
majority of you simply could not understand why, despite all the
money invested and the level of the technology in F1, that this can
still happen. Also, I’m sure that you would not understand why this
seems to happen more often to the biggest team!
I will try to offer a concise and simplified list of the major
reasons behind this dilemma. Like the famous ‘Sword of Damocles’,
it undermines the serenity of all the aerodynamicists and all of
their colleagues involved in the development process. But before,
please let me clarify the meaning of word “correlation” that is, in
some cases, confused if not abused.
Correlation means a mutual relationship or connection between two
or more things. Ok, so: firstly we talk about relationship and not
about equality (i.e. not a “perfect repeat” to be expected);
secondly, for the matter of this article, the “two or more things”
are a calculation, two or more experiments and a person. Sorry, say
again please? Sure: the relationship/connection to find is between
CFD results, measurements from wind-tunnels, track measurements,
and the driver feedback.
Generally speaking however, the four environments are not put in a
relationship at the same moment. As a “rule of thumb”, being
perfectly aware of the crude limitation of any rule done by
thumbs!, the first relationship to find and “secure” is between CFD
outputs and wind-tunnel results. That second tool is still in
the majority of cases of aero development, the “final word” for
what will be sent to production for track test and, hopefully, to
be finally raced. But not always: there are, in fact specific and
peculiar aerodynamic aspects (see for instance thermal effects like
brake- and engine-cooling, or specific flow behavior like those
related to flow-features involved in the rear wing behavior) for
which CFD is nowadays considered the absolute reference, due to the
constant improvement of the model and the intrinsic limitations
related to a wind-tunnel experiment.
By far, when the tunnel-to-track correlation is suffering, the
implications are vastly more serious and, generally, the solutions
are expensive and time-consuming. This shouldn’t be big news for
most of you (the braver readers should have noticed the usage of
the plural when talking about wind-tunnels two paragraphs above):
teams are now used to performing aero experiments in more than one
facility. Do two tunnels “say” the same? Well, obviously no. In
worst cases, with reasons that are behind the scope of this
article, seriously conflicting results are the very first dilemma
to solve if/when this happens. Result-conflicts would never become
100% agreement for all types of aero test, but experience and time
(and patience…) generally helps to define a robust strategy to
correctly manage the development in two or more tunnels and to
elect the “master” facility for a specific item/area of the car to
develop. In some cases the other two environments (CFD and track)
can work as “referee” to support this decisional process.
The synergy, and not the competition, between CFD and tunnel
activities is the key-factor for the aerodynamic development to be
carried out as much successfully as possible. This item alone would
merit a dedicated article, which I promise to think about…
With the above exceptions, the results from the tunnel, hopefully
supported by the already-set correlation with CFD, are finally
compared to the feedback arriving from the car: this step involves
both measures (thanks to all the sophisticated sensors which a F1
car is now equipped with) and the driver “opinion”. The latter, as
you should easily imagine, sometime can be “definitive”, despite
not always as scientific as the engineers would expect. But please
remember that there is not, and there will never be, any
simulator/sensor, system, engineer’s ability in data
analysis/data-interpretation, routine, etc… that is able to give
feedback on the “overall car behavior” at the level of a
top-driver. Who is called upon to list the pros & cons of a
specific modification to the car? Absolutely, his feedback deserves
trust but, being subjective anyway, needs correct interpretation by
experienced engineers. When the driver’s feedback agrees with the
evidence of the data or, even better, is able to complete what the
data cannot say (limited exercise, read after please)… bingo!
Hold on, and the lap-time? Well, despite this appearing illogical
to you Gents, lap-time is important, but quite rarely is it the
first figure to look at when deciding if a new aero-package is
“better” or not. The lack of time for testing a new configuration
in different moments of the day coupled with the fast-changing
nature of the track and tires (there they are again!!!), make lap
time based judgment quite difficult, if not risky in some
circumstances. Please be aware that, in the majority of cases, the
claimed improvement in terms of lap-time is in the order of few
tenths.
Before proceeding, please let me digress a bit? The current lack of
testing imposed by the Sporting Regulations, has a consequence that
should be evident to lots of you and is a topic that is seriously
debated. That is a different story; hence I will not offer a deep
comment here. Just let me say that in any competitive exercise,
what is limited somewhere is compensated for somewhere else. Those
who have bigger resources can react faster. In F1, that is an
extremely competitive exercise, the progressive reduction of track
testing was surely responsible of the proliferation of all the
off-track jigs and simulators, whose level and sophistication has
improved massively in the last few years. It’s a very interesting
challenge for any engineer, but, I’m not so sure if the final
result on an economical basis was the best answer ever. Think about
the ultimate spirit of motorsport, where the word “sport” is still
at the same level as “motor”, correct? More testing opportunity,
even if regulated and optimized (on a Monday following the GP, for
instance) should not to be too expensive and should be given back
to Teams. While writing Teams and Federation seem to find an
agreement for a wise re-introduction of track test starting from
2014. Definitively, this is a positive new.
Back to correlation now! As you already can imagine dear readers,
the correlation-exercise is quite complex to control. And while
correlating tunnels to track, that is the core-business of this
exercise, all should reckon that two experiments are involved here,
each of them with their own experimental errors, limitations and
levels of uncertainty. These aspects have to be taken into account
carefully; otherwise the comparison will not be fair (i.e. a
fundamental error of approach would be made). But there is another
important aspect when dealing with aerodynamic correlation in F1,
this not always being easy to remember, even for some of the
insiders: CFD, tunnel(s), and track are environments with strong
specificities.
A CFD run would tell us everything about the complex features of
the flow around the car (flow path lines, vorticity levels, wakes,
flow recirculation’s and separations, internal aerodynamic
features, single-part contributions, effect of unsteadiness, etc… )
around a CAD-originated “virtual car” in a fixed set-up, perfectly
“rigid and stable”, immersed in a empty space and running on a cold
smooth-floor which speed is synchronized with the free-stream, with
controlled level of turbulence managed by a mathematical model; and
when run-time and cluster-size is not an issue, flow unsteadiness
and thermal effects can also be turned-on to improve the realism.
Finally, due to the specific requirements of the dev-program in
CFD, the calculated configuration is never 100% equal to those from
either tunnel or track: some differences are tolerated by
experience, when experience does not become a high risk decision to
take.
At the same time, the wind-tunnel experiment (using a hand-made
scaled-down model replicating the reference configuration as
perfectly as possible) would tell you about the evolution of the
aerodynamic forces, internal flows and surface-pressure while
changing the car’ “attitude”, i.e. varying front and rear rides,
steer angle, roll and yaw angles; five variables properly combined
during a tunnel run that can be the result of a sequence of fixed
combinations or obtained by synchronized slow-motion movements of
the above five parameters. But the experiment in the tunnel implies
that the real physics is reversed (model stationary inside an
“moving-air pipe”, hence in a confined space, where the air and the
“ground”, this with limited dimensions…, runs at same speed, fixed
to a specific value) and, normally, no thermal effects are
involved. Also, the model is inevitably less accurate than the real
car and not “perfectly rigid”, hence local deformations (not all of
them under control, unfortunately!) are inevitably present. And
what about “tires realism” and related limitations? Well, this is
such of a fundamental aspect that a specific article was devoted on
the matter by the writer, please refer to it. Last but not least in
this environment, and for similar reasons as for CFD, the model
configuration would normally differ “a bit” from those from both
CFD and track. Again, the experience should (should!) indicate
which level of difference can be accepted not to have results in
conflicts with those from the other environments…
Finally we arrive at the track, where all is “real”. Real speed
variation, real lateral and longitudinal accelerations, real wear
of components (tires above all, here they again!!!) and
speed-dependant part deformation, real details and split-lines
between bodywork-components, real heat-exchanges phenomena to cool
the internal components, real track surface and its status-changing
including induced effect on the air-layer close to ground due to
tarmac temperature, real variability of weather conditions (wind
above all…), real driver ability/mistakes, real helmet motion, etc,
etc… Last but not least, “real” is the limited capability of
measuring both the car’ downforce (the contributions from the four
wheel-groups are lost because directly bridged by the ground) and
its aero-drag, the latter being indirectly derived by assuming
engine-power and rolling-resistance of tires (stop talking about
tires!!!).
All this is to say that, while correlating the factory-based models
(CFD and/or tunnel) with track, a “common language” has to be
established. Otherwise the exercise would risk becoming a
sort of guessing game and quite often a cause of painful
confrontation…. In other words, similar conditions have to be
ensured if at all possible, and the un-removable differences need
to be recognized and known in terms of effects, for them to be
taken into account very, very carefully.
This is why, for instance, teams are used to perform peculiar
aero-test going up and down on a straight-line, at fixed speed and
controlled ride-heights, with the aim to be “closer” to CFD and
wind-tunnel to verify their claims. Probes, with different
dimensions and aims, are quite often installed around the car to
“interrogate” the surrounding flow, this to extend the
figures to look at while correlating (see the picture here above!)
. Due to the already-commented limitations imposed by the
sporting rule, this peculiar test is sometimes also carried out
during the GP weekend (track lay-out, general condition and
“traffic” permitting). Problem is that this sort of “full-scale
wind-tunnel” cannot simulate, by definition, the aerodynamics
involved in braking and cornering conditions, which is even more
important than the aero-performance during the acceleration-phase
along the straight. In the majority of F1 tracks in fact, due to
their modern lay-out, the lap-time primarily comes from these two
key-maneuvers, for which the correlation is still not at the level
achieved for speed&rides controlled straight-line testing.
No problem, the braver drivers can compensate by giving us
useful feedback!
It’s a complex exercise, isn’t it? Yes, but not impossible to solve
or, better, “control”. The secret is methodology, organization and
innovation. Robust methods and procedures should ensure that the
data-comparison between the environments involved is constant and
well under control. This should feed the process, thanks to
knowing which methodology has a stronger correlation to which
aerodynamic area of the car. Well-defined and well-followed
procedures should help maintaining testing environments in order to
avoid undesired effects on the data (issues that, unfortunately, if
happen will not be immediately evident). Secondly, organization
means that a specific team of people has to constantly deal with
these aspects, devoting their work-hours to looking after the whole
data-chain and the tools for post-processing, ensuring pro-active
interactions with colleagues fully immersed in CFD, tunnel and
track works. Finally, innovation means promoting any technology
helping to improve the realism of both CFD and tunnel(s), to
elevate the precision of all of the measures and the maths behind
them, to maintain the testing quality at the highest level and to
extend the domain of what is possible to measure at the track.
These technologies need to be constantly considered, validated and
adopted.
Correlation is not something that can be mysteriously lost or
magically improved, as sometimes seems to emerge from the press. F1
engineers are well aware of the implications of the peculiar
approach and the compressed-timing dictating by high-level motor
racing, hence they are prepared to accept, despite no perfect
reasons can always be offered, periods where the relationships with
track-results is not as satisfactory as it was. Personally, I’ve
learned more from poor-correlation periods than from the
issues-free ones. It’s the perfect occasion to identify which
elements of the global process are still “lacking”, i.e. where
directing your resources, and/or if a specific aerodynamic concept
is still not adequately supported by pre-track analysis: in other
words, not fully-understood!
And please, do not be surprised if the biggest teams seem to suffer
more by this issue than the minors. Two main reasons behind:
firstly, they “are in news” more than the others; secondly, the
main aspect, their mission is to push harder, delivering
aero-updates with greater frequency and nature (very often “on the
edge”) and that makes them more exposed to correlation
“fluctuations”.
But, believe me; if they are always able to start from the first
rows of the grid, it is because the overall level of their
correlation is, on average, much better than what it sometimes
seems to be!